材料の選定
あらかじめ考え抜いた設計に従って作業を進めてゆく。まずはらせん階段を作るところから始める。
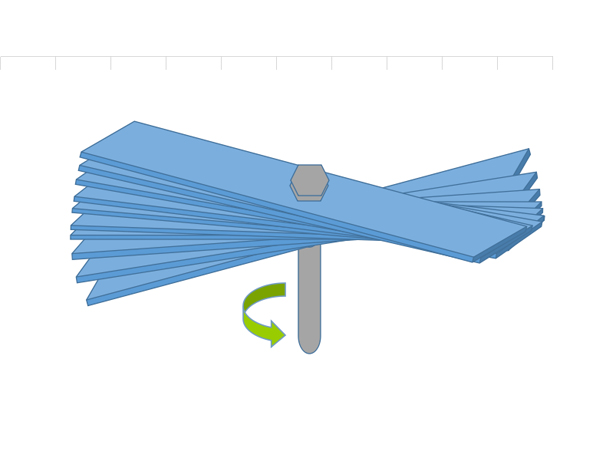
材料は厚さ3mmのアルミの板である。ホームセンターで買い占めた。300mm×200mmが2枚、300mm×100mmが2枚あった。
なぜアルミなのか? FRPの方が簡単に作ることができて、軽く仕上がるのではないか? しかしそこには素人なりの考えがある。プロペラが漂流物にぶつかったとき、あるいは浅い場所で海底をこすってしまった場合、アルミなら歪みはするだろうが、割れたり折れたりすることはないだろう。多少性能が落ちたとしても、、ビーチに帰るまではそのまま使える。これがプラスチックの場合、割れてしまうと航行不能になる。もとより非常時用のオールは積んでおくつもりだが、できれば使わずに済ませたい。
反面、アルミは海水により腐食する。したがって、塗装については念入りに施しておく必要があるだろう。しかしそれは何とかなるのではないだろうか。
らせん階段の作製
アルミの板を、まずは幅25mm、長さ300mmに切る。そうすると、購入したアルミ板からは、24枚の細長い短冊が手に入る。その中心に、ドリルで直径12mmの穴を開ける。そして24枚の短冊を、M12のステンレス製ボルトに挿して、積み重ねるのだ。
幅25mmの短冊によってらせん階段を作るということは、スクリュー・プロペラのブレードの中心部が25mmもの厚さになるということだ。タンカーのスクリューじゃあるまいし、厚すぎないか? ま、いいか。後で削ればいい。そう思ったのは大変な間違いだった。中心部の穴が直径12mmであれば、短冊の幅は18mmで十分だった。それを25mmにしたことによって、分厚いアルミの塊から薄いブレードを削り出す、気の遠くなるような作業を強いられた。しかしそれはずっと後の話である。
ともあれ、アルミの板を切って穴を開けるこの工程には、約1週間かかった。
次に、作り終えた24枚の短冊を、M12のステンレスボルトに挿し、少しずつずらしながら積み重ね、らせん階段状に接着してゆく。エポキシの2液式接着剤を使った。アルミは接着剤が効きにくい素材ではあるのだが、ボルトがシャフトとして貫いているので、接着剤が剥離する心配はまずあるまい。
短冊をずらす距離は、1枚当たり、外周部で7mm。ブレードの傾斜角を外周部で23°とするためには、正確には6.79mmなのだが、接着剤で手をべたべたにしながら、そのような精密な寸法は出せない。おおまかに、7mmとするしかない。
1枚3mmの厚さの短冊を24枚重ねたのだから、理論上は、このらせん階段は高さ72mmとなる。間に接着剤の層があるので、多少は伸びる。実測で75mmだ。これがスクリュー・プロペラの厚みとなる。
この時点で、重さは約2kgもある。ずっしりと重いこの感触に、とっさに「あ、失敗した」と思った。幅25mmの短冊はやりすぎだった。その分だけ削る量を増やしてしまった。中心部が25mmなのはまだいい。しかし徐々に薄くなってゆくブレードの外周部でさえ、厚さ10mmを超えているのを見て、気が遠くなった。これを厚さ1mm程度に削らなくてはならない。いったいどれだけ削らなければならないのか。最終的にはプロペラの重さを半分に、せめて1kgを切る程度にまでしなければならない。大変な作業だぞ、これは。
まあ、いい。厚さのことは置いておこう。それより、できあがったこのらせん階段、段差がかなりの凹凸をなしている。まずはそれを削って、なめらかな曲線に仕上げることが先だ。薄くするのは、その後だ。