船体の法則性
海面に浮かべた2つの物体。話を単純化するために、ここでは直方体だとしよう。
まずは最初の考察だ。この2つの直方体は、同じ材質、同じ体積である。したがって、比重、質量も同じである。比重は海水に対して0.5だとしよう。すると両方とも、体積の半分は海面下に沈み、半分は海面から出ている。浮力も同じだ。同じ重さの物体をその上に載せて、浮いていることができる。
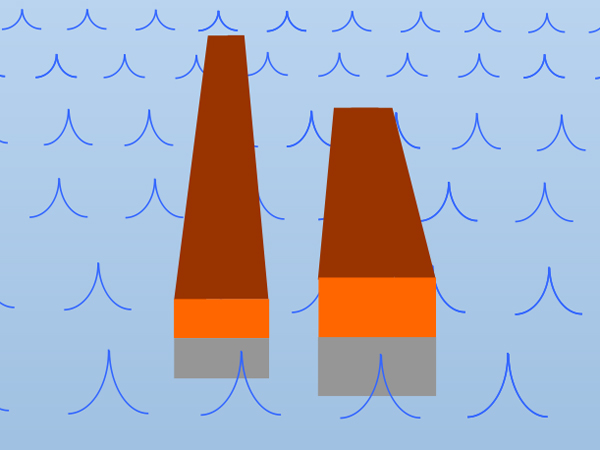
左は細長く、右は短くて太い。左は右の2倍の長さだとしよう。その結果、断面積は左は右の半分となる。比重が同じなので、海面下に沈んでいる部分の断面積も、左は右の半分だ。
この両者が海面を移動する際、抵抗となるのは海面下に沈んだ部分だ。その抵抗は、たぶん、造波抵抗と呼ばれるものだ。その大きさは進行方向の断面積に比例し、左は右の半分となる
この法則性によれば、船体は長ければ長いほどよいということになる。しかし、長すぎる船体は、3つの点で問題がある。1、車に載せて運べない。2、強度が落ちる。3、直進性が強すぎて回頭性が悪く、小回りが利かない。したがってその長さにもおのずと制約はある。
次の考察だ。全く同じ形、同じ体積で、材質の異なる2つの物体がある。この2つは質量が異なる。したがって比重が異なり、水面下に沈んでいる部分の体積、断面積が異なる。
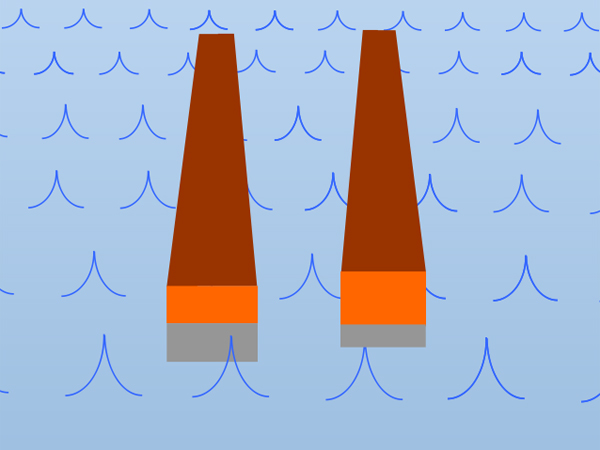
左は海水に対する比重が0.5だとしよう。右は0.25だ。すると、海面下に沈んでいる部分の断面積は、右は左の半分だ。したがって抵抗も半分だ。
ここで、上の図の右と下の図の右を比べると、抵抗は半分のさらに半分で、4分の1となる。つまり、長さと軽さは相乗効果となって、抵抗を減らす効果が著しく増すのだ。
それだけではない。船体の幅が同じだとして、長さが2倍になれば、先端の角度は半分になる。
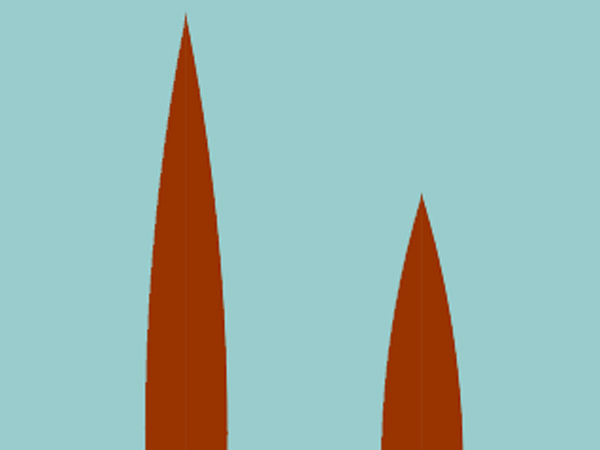
その鋭角さが、さらに抵抗を減らすのだ。したがってこれは相乗効果の上を行く、三乗効果になるのではないか?
これから作る船体の長さは、2分割で車に積める最大値の2m40cm。つなげれば4m80cmにもなる。なおかつ、前作よりも細く、幅30cmで、高さは20cmだ。これでだいたい前作と同じ体積、同じ浮力となる。
だから、前作よりも軽くはならない。材料は前回と同じT1・3mm厚の合板で、パネルを張り合わせる外殻構造だから、重量は使った合板の面積に比例する。細長くすれば、体積に対する表面積の比率は増す。つまり、重くなるのだ。
しかし、船体だけではなく、機関部も含めたボートトータルの重さを抑えることができれば、前述の三乗効果は得られる。そこを目指すべき着地点として、まずは船体から作り込んでいくことにした。
船体の作製過程
芯も節も持たない、完全に中空の、外殻だけの構造。その分軽くできる。それを目指したかった。しかし内骨格なしで、合板を適切な形に切り抜いて貼り合わせるだけの工法だと、まずは精密な展開図を描く必要があった。応力の分析も必要だ。それが私の頭脳には荷が重かった。まだまだ経験が足りない。本番の前に厚紙で10分の1モデルを何度も作ってから取り掛かるべきだった。しかしその時間がなかった。
だったら、それを脇に置き、今回の取り組みで一番やりたかったことを優先するしかない。それはなだらかな局面で構成されたシャープな形状の実現である。これはこれでとても難しい。同時に2つは無理だ。完全に中空な船体を作るのは、次の第4期に譲ることにした。
最低限の芯と節で外殻の形状をコントロールし、船体を形作ってゆく。横方向の節の数は2つ。縦方向には中心に背骨を1枚。これを骨格として、パネルを貼り合わせてゆくのだ。
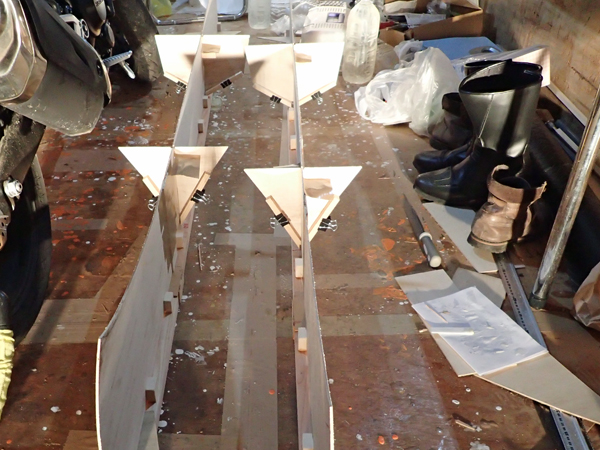
船首は切り立ち、尖っている。そこから船底に向かってなだらかに水を押し広げる。そういう曲面。そのためには合板にひねりを加える必要があった。しかし、ひねりを加えると、合板には歪みが生じ、船首が上に反り返ってしまう。そこで私は考えた。幅の広い合板を無理に捻ろうとするから歪みが大きいのだ。だったら合板を細長く何枚もの冊に切り分け、捻りながら接着していけばいい。
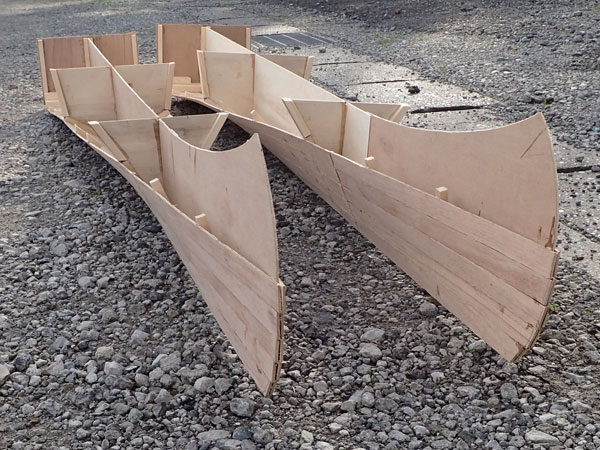
この方法はとても手間がかかるやり方だったが、歪みは上手く逃がすことができた。船体の作製については、この点以外に目新しいものはない。
エポキシの硬化不良の克服
前回の取り組み=「第2期」においては、エポキシの硬化不良に悩まされた。船体にエポキシを塗布すると、何日たってもエポキシは完全に硬化せず、表面がネチャネチャしたままだった。気温が低いのかと思って太陽に晒して温めてもダメ、主剤と硬化剤の比率2対1に誤差があったのかと思って厳密に計ってもダメ、撹拌が足りないのかと思ってどんなに撹拌してもダメ。最後には雑巾で水拭きして、ネチャネチャの表面を除去しなければならなかった。
しかし、今回分かったのは、それで正解、そうするしかなかったのだ。
ネチャネチャの正体は、硬化不良を起こしたエポキシではないのだ。エポキシが浮き上がらせた合板の脂に違いない。他にも合板メーカーが製品を製造するときの接着剤、あるいは私が合板を貼った時の接着剤、そういった不純物も含まれているかもしれない。
塗ったエポキシにそれらが溶け出し、内側から表面に向かってエポキシが硬化した際、それの不純物が表面に浮いて、ネチャネチャするのだ。そう考える根拠は、2度、3度とエポキシを重ね塗りするたびに、ネチャネチャが消えてゆくからだ。
だから、何らかの方法でこのネチャネチャを除去しなければ、それはエポキシ塗面の堅牢さを阻害する。その方法は、雑巾で水拭きが正解だ。なぜならこのネチャネチャは水溶性、あるいは水和性があり、水拭きで簡単に除去できるからだ。
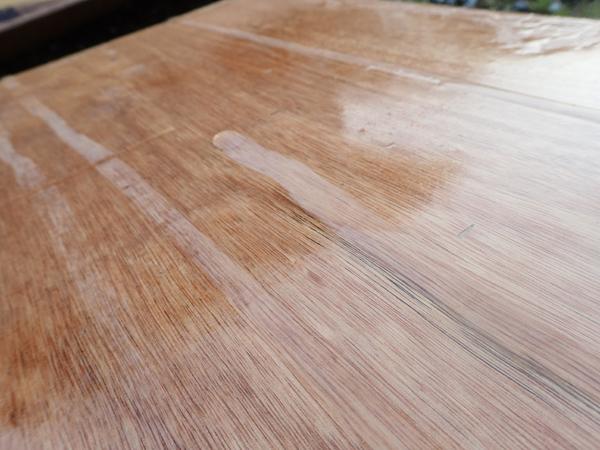
写真は、船体に塗ったエポキシが十分に硬化したのち、塗面に水を流した様子だ。水が流れた跡が即座に白濁する。それを濡らした雑巾で拭うと、雑巾はたちまち黄色く汚れる。エポキシも、主剤は透明でも、硬化剤は黄色いのだが、2液を混ぜた状態でここまで黄色くはない。したがってこれは硬化不良を起こしたエポキシではない。合板から染み出した脂に違いないと思ったのだ。
ネチャネチャを雑巾で拭うと、消しゴムのかすのようなものがぽろぽろと出てきて、雑巾にへばりつく。その下には硬化したエポキシ面が現れる。
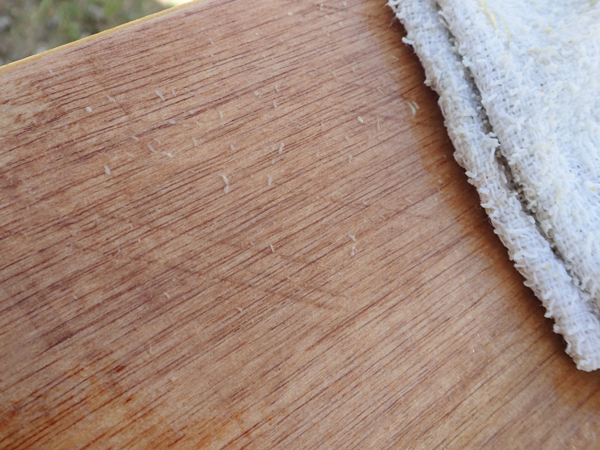
それでも表面はまだ多少べたつく。完全に除去できていないのだろう。しかし2度、3度とエポキシを重ね塗りし、そのたびに濡れ雑巾でゴシゴシ拭うと、べたつきは、やがて完全に消えてゆく。そのようにして使った雑巾は、数か月後にはごわごわに固まる。脂が酸化して硬化するのだろう。
ピンホール問題の解決
合板を貼り合わせた船体にエポキシを塗ったとき、気温の変化によって中の空気が膨張と収縮を繰り返し、いわば呼吸することによって、塗面に小さな穴を開ける。合板の接合面に僅かでも隙間があると、そこに穴ができやすいが、合板面の中央部にだって、ブクブクと泡を吹きながら穴ができる。この穴を塞ぐのは、エポキシの重ね塗りなんかでは無理だ。ずっと粘度の高いパテを使わなければならない。いや、その前に、こんな穴は開いてほしくない。
この問題をどうするか。逆転の発想だ。最初に大きな呼吸穴を確保しておいてやる。船体の両端に2つ。そして船体内の節にも穴を開けた。したがってこの2つの穴は通じていて、片方から息を吹き込むと、もう片方から空気が出てゆく。
こうすると、接着剤やエポキシがまだ硬化しないうちに、気温の変化で船体内の空気が膨張したり収縮したりしても、この呼吸穴から空気が出入りし、あちこちに穴が開くことがない。最後に、エポキシの重ね塗りが終わった段階で、この呼吸穴を塞げばいい。穴の場所はあらかじめわかっているのだから、パテを使って確実に塞げば、それで完了、他に穴はない。
喜ばしいことに、この方法には、最後にこの呼吸穴を使って、密閉性を検査することができるという、副産物もあった。
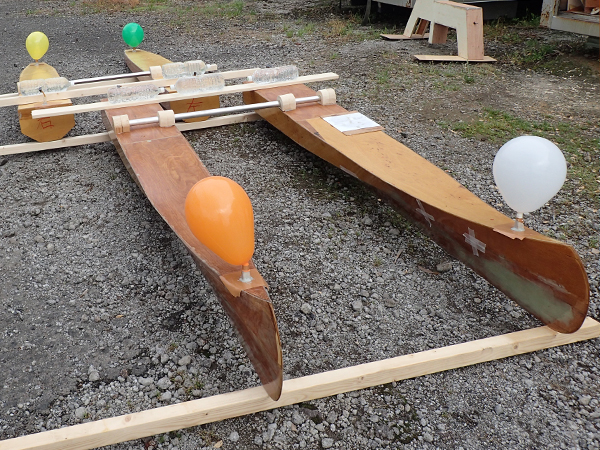
上の写真は、2つの呼吸穴に管を挿して、その片方にゴム風船を被せ、反対側の呼吸穴から息を吹きこんで、風船を膨らませたものだ。これは密閉性の検査を行っているのだ。この風船が、例えば1時間おいてもしぼまなければ、船体は完全に密閉されており、海に浮かべても浸水しないことが保証されるというわけだ。
ただ、この検査には悩ましい問題点がある。ゴム風船そのものが、単体でも、一昼夜も置いておくと、しぼんでしまう。だから1時間しぼまなければOKとはいえ、念には念を入れて、一昼夜しぼまなければもっとOKとはいかないのだ。まぁ、船体に開いた小さなピンホールでも、1時間はもつまいと思うので、1時間もてば合格と考えていいとは思うのだが。
船体の塗装
塗装についてはまったく経験が足りない。もっといろんな経験を積みたい。何か新しいことを試してみよう。
第1期のボートには、アクリル系の水性エマルジョン塗料を使った。あれは乾燥後にも塗膜に柔軟性があり、クルマの中で重ねると、塗面同士がくっついてしまう。水性だからとても扱いやすくてよかったのだが、難点が大きすぎるので、もう使わない。
第2期には、2液式のウレタン塗料を使った。プロが使うような高価なやつだ。あれはさすがにしっかりしたものだった。よく伸びて塗りやすく、強固な塗膜を形成した。問題点は、ペンキ屋で取り寄せてもらわなければ手に入らないことと、値段が高いことだ。
第3期となる今回は、シリコン系の水性塗料を試してみることにした。ホームセンターで、とても安く手に入る。水性だから扱いやすいし、シリコン系はウレタン系よりも高耐久だと聞いている。
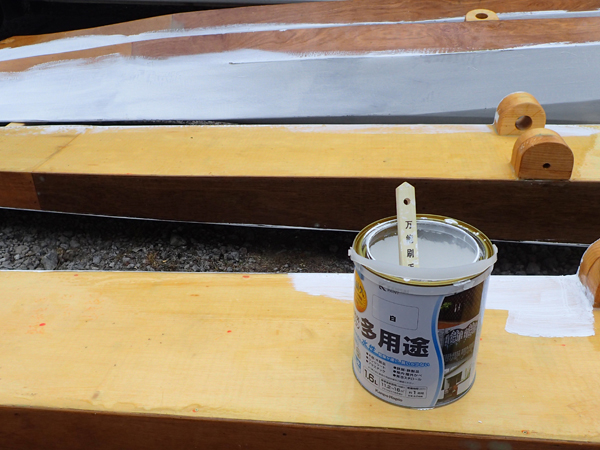
しかしこれは失敗だった。水性だからだろうか、下地のエポキシとの相性が極めて悪い。塗って乾かした後、ちょっと擦るとすぐに剥げる。何度重ね塗りしても、丈夫な塗膜にはならなかった。
やはりあの高価なプロ用ウレタン塗料にはかなわないのだ。
新方式のジョイント
ジョイントとは、分割した船体の前後2つをつなげることだ。分割して車に載せ、出航前にビーチで組立てる。ジョイントはそのためのものだ。
このジョイント部に、前作のように木材の支柱(当て木)を使ったのでは、重量が重くなり過ぎる。前作ではそれだけで、左右併せて6kgあった。それもそのはず。丈夫な木材を、表裏×左右の4本も使ったからだ。
それにあの方法では、組立てや分解に際して、ナットを締めたり外したりする箇所が多くなる。それはとりもなおさず、準備や後片付けに要する時間が長くなることを意味する。それをもっと簡単にできないものか?
そう考えて、蝶番を使ってみることにした。接続部に補強を入れ、蝶番をねじ止めする。その蝶番は、ホームセンターで売っている中で最も頑丈な、ステンレス製のものを選んだ。それでもネジが飛んだり、歪んだりするだろうか? いや、そっと曲げ伸ばしするように気を付ければ大丈夫だろう。
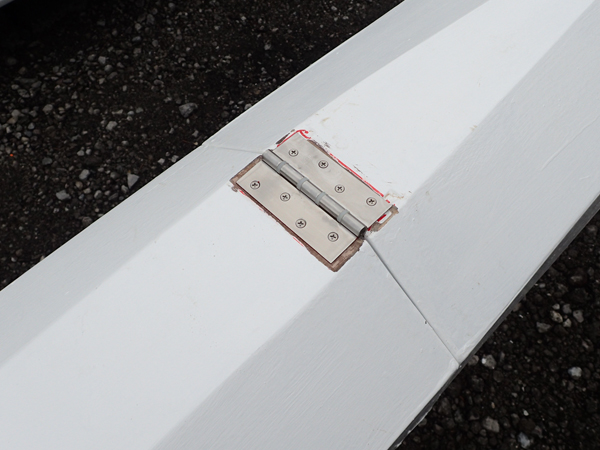
しかし、これは予期せぬ問題を発生させた。船体は前後に2分割した状態では8kg強の重さだった。この重さなら運搬するにも大したことはない。もっとも、4回に分けて何度もクルマと波打ち際を往復することになるのだが。
それが、蝶番で前後2つをつなげてしまうと、重さは約17kgになる。まあ、重量的には耐えられる範囲だ。しかし蝶番によってブラブラする、2.4mもある、半固定の2本の物体を運ぶのは大変だ。とくに車から降ろす時、あるいは載せるとき、折れ曲がった船体の両方をしっかり支えないと、蝶番が開いてしまう。そうすると、開いた船体の先端は、半径2.4mの円運動で地面に激突するのだ。これは相当な衝撃だ。
しかし、ちょっと待てよ。ここは考察が必要だな。問題の本質はどこにある? 蝶番か? それとも船体の重さか? 船体をもっと軽く、コンパクトに作れば、この問題は解決するのではないのか?
ところで、固定の強度は全く問題がない。船底側に蝶番、デッキ側にはボルトとナット。これだけで前後の船体は、まるで継ぎ目などないかのように、しっかりと固定される。
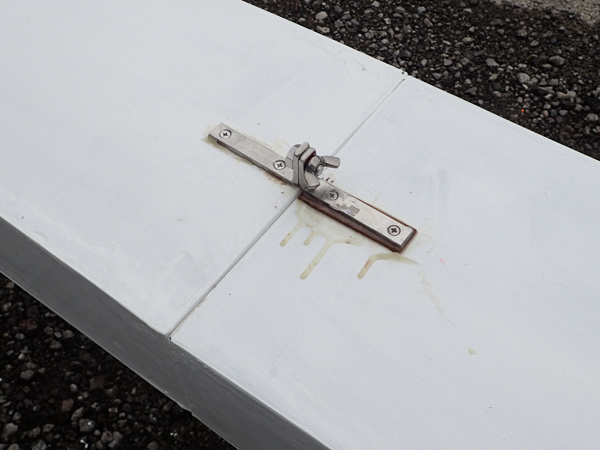
これでずいぶんと軽量化にはつながったはずだ。
ステンレスの支柱
さて、次は船体最後の工程、左右のジョイントだ。前回はここにも木材の支柱を使った。船体の中央部に、80cmの間隔を開けて、2本。それぞれは2kgあるので、併せて4kg。今回はそれを直径32mmのステンレスパイプに換えることにした。そして2本の間隔を120cmと、もっと開けることにした。
この支柱、木材だと、十分に頑丈にするために、重くなりがちなのだ。なぜなら木材は破損するときは裂けるので、破損が即座に航行不能につながるため、絶対に破損は許されないということだ。しかしステンレスパイプなら、過重な力が掛かった場合、まずは曲がる。曲がって耐えてくれるのだ。したがって多少破損した状態でも、岸に帰るぐらいは持ってくれるに違いない。だからステンレスパイプなら、重さを、必要な強度の範囲ぎりぎりに抑えることが可能なのだ。
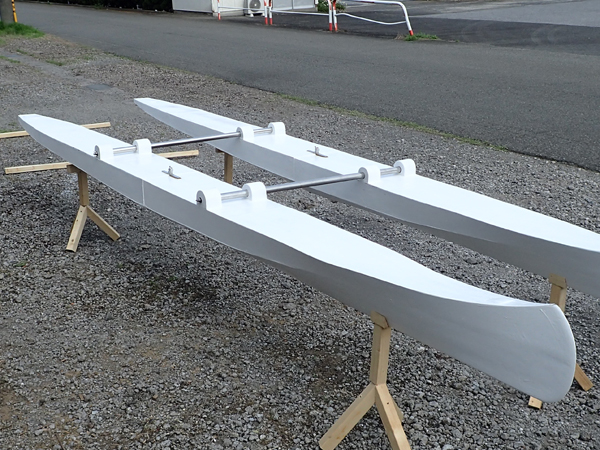
ステンレスパイプの長さは、船体の幅である120cm。重さは2本で約1kgだ。したがってこの部分で3kgの軽量化を果たしたことになる。
船体での軽量化の成果
これで船体は完成だ。前作からどれだけの軽量化ができただろうか?
前作では、船体4ブロックが、それぞれ7kg。前後のジョイントが、片方3kg、左右併せて6kg。そして左右のジョイントが、支柱1本あたり2kg、2本で4kg。したがって
7kg×4本+3kg×2本+2kg×2本=38kg
それに対して今回は、船体前後のセットで17kg、それが左右に2列で34kg。前後のジョイントは船体に含まれており、左右のジョイントは1本あたり0.5kg、2本で1kg。したがって
17kg×2本+0.5kg×2本=35kg
船体の長さを3.2mから4.8mへ、1.5倍もの長さにしたのに、重量は逆に3kgの軽量化。もっともっと軽量化したいが、それは強度不足と隣り合わせのリスクを背負うことになるので、第4期の課題とし、今第3期ではこれでよしとしよう。