スペースの問題
今やろうとしていることは、旧型のアンバサダーに新型の高速ギアセットを移植し、なおかつ、新型では省略されたドラグクリックを復活させようという企てだ。クリックが鳴る仕組みは単純で、ピンとギアの組み合わせである。
どのパーツにピンを、どのパーツにギアを仕込むかという問題は、それはそれで悩ましい問題だった。私はそれを平面的な設計でなく、最上部のドラグワッシャーの3層立体構造化によって、理想的な形で解決した。そうすることによって、パーツ構成やギアとの噛み合わせの形状は変わらず、機構全体の働き方を変えることがなかった。
このことは重要だ。メインギアそのものには全く手を加えたくなかった。そうであればこそ、ギアがすり減ったら交換するだけで済む。そのたびに四苦八苦の加工をする必要はない。やたらと手間と時間を食うこの地獄の作業は、今回のたった1回で済むのだ。
しかし、あらかじめ覚悟をしていたひとつの難問が立ちはだかる。ドラグ機構を含むメインギアユニットを格納するための、スペースの問題だ。
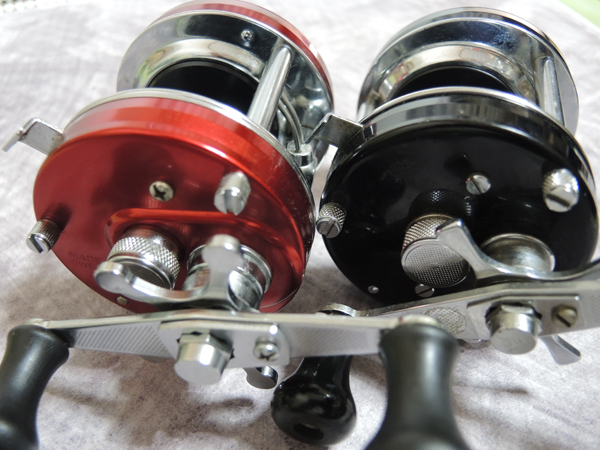
上の写真で並んでいる2台のアンバサダーは、黒い方が旧型、赤い方が新型である。同じ形状で同じ名称の5500Cだが、機構の違いに由来する外観上の区別が3つある。新型にはハンドル基部にポッコリとしたふくらみがあるが、旧型にはそれはない。プッシュボタンの押下面の角度が、新型の方が寝ている。ハンドルと本体との距離が、新型の方が開いている。
このうち、1つ目のポッコリとしたふくらみに着目しよう。このふくらみをもたらしたのは、ドラグ機構が厚くなったためだ。私の研究によれば、それは新型のマルチディスク化を直接の理由にしたものではなく、旧型と新型の過渡期に存在したドラグのサンドイッチ化を直接の理由にしているのだが、そのことはここではどうでもいい。重要なのは、新型のドラグ機構も、このポッコリとしたふくらみを必要としていることだ。そしてそれはもちろん、カップ内に、分厚いマルチディスクドラグを納めるためのものだ。
もし新型の分厚いドラグ機構を、旧型の平坦なカップ内に収めればどうなるか? その実験をしてみたのが、下の動画だ。結論から言えば、カップは閉じることができるが、ドラグ機構の最上部に位置するワッシャーがカップに接触し、異音が発生する。残念ながらこのまま使うことはできない。機械には本来わずかな遊びが必要だから、それを加えても、足りないスペースはほんのコンマ何ミリ。それがあのポッコリの理由だ。
ブレーキ材の薄型化
どうすれば、マルチディスクドラグ全体を、1mm弱、薄型化することができるか? その寸法をかせぐには、機械的強度を低下させないために、ステンレスワッシャーを薄くすることはできず、もはやブレーキ材を薄くするしかあるまい。その考察のために、マルチディスクドラグの構成を再度確認してみよう。
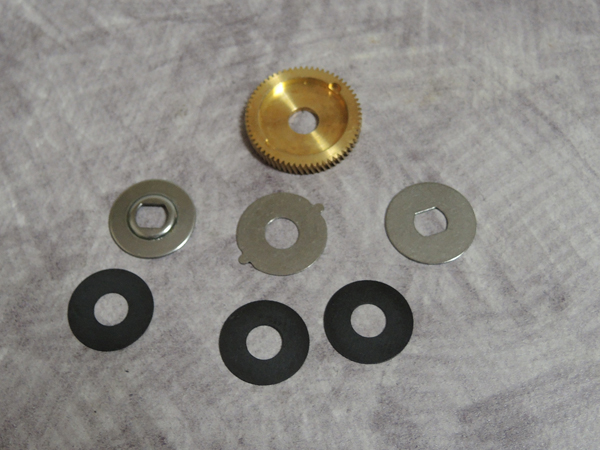
写真のとおり、3枚のブレーキ材(下の黒い樹脂製のワッシャー。最新型ではカーボンファイバー製のもの)が使用されている。1枚当たりの厚さは約0.5mm。これをわずかずつ薄くすれば、コンマ数ミリは簡単に稼げる。
ところが、一番下のブレーキ材を薄くすることができない。なぜならギアに掘られた耳型の窪みが、ギアの底まで到達しておらず、したがって耳付きのステンレスワッシャーの位置を下に下げることができないのだ。したがってメインギアに接する一番下のブレーキ材には、手を付けることができない。
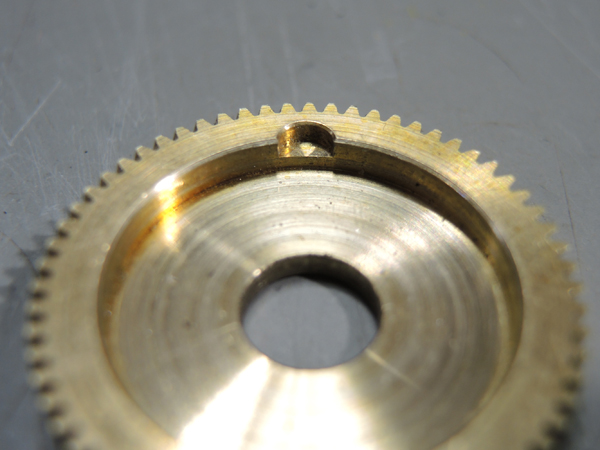
とすると、残りの2つのブレーキ材を薄く作らなくてはならない。すなわちそれは耳型の突起のあるステンレスワッシャーを上下から挟む、2枚のブレーキ材だ。
ところで、このワッシャーにはギアを刻んだため、ブレーキ材と摩擦する面積が大幅に減ってしまった。このことはどのように影響するだろうか? それを考察したのが、下の図だ。
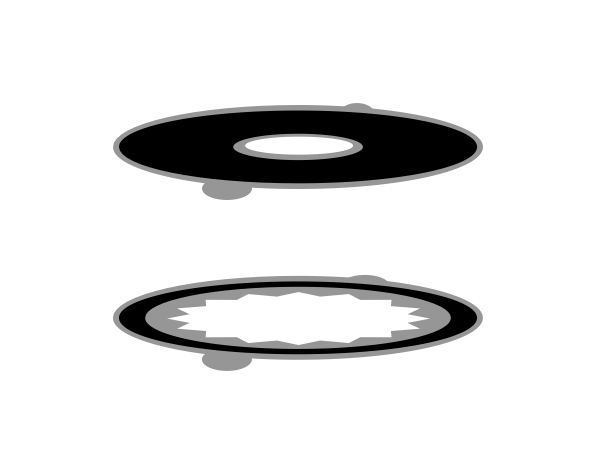
図の下のモデルのように、ブレーキ材の面積が減り、ワッシャーの外周部に偏ったら、ドラグ性能はどうなるのか? 上のモデルと比べて摩擦材の面積は減るが、そのことによって、摩擦が減るとは言えないだろう。なぜなら狭い面積に圧力が集中することによって、面積単位当たりの圧力が増すだろうから。したがってドラグノブを締めこむ力が同じなら、発生する摩擦力は、上下のモデルで理論上は変わらないだろう。それより、ワッシャーの外周部にブレーキ力が集中することによって、作用するドラグ力は却って増すに違いない。
他方、ドラグの滑らかさは損なわれるかもしれない。例えば、滑り出しが悪くなるというような。その懸念は、私の釣りには何の問題もない。
以上の考察を経て、私は自信をもって、ここからの作業を進めることができる。
ブレーキ材の材質
ブレーキ材には、繊維と樹脂の組み合わせが適している。例えば旧型5500Cのブレーキ材は樹脂を含浸させた皮革である。しかし皮は厚くなるから、今回は使わない。以前から今回の改造ではブレーキ材として、極限まで薄くすることのできる紙を使おうと決めていた。紙とは、すなわちセルロース繊維である。そこに樹脂を染み込ませればよい。
紙が弱いという懸念は全くない。本来セルロースは強い繊維だ。濡れた紙がボロボロになるのは、セルロース繊維が破断するからではなくて、剥離するからに過ぎない。したがって、樹脂を含浸させて繊維同士を固めれば、剥離は解消でき、水濡れにも強くなる。
紙に含浸させる樹脂には、接着剤を使う。エポキシ系がいいか、アクリル系がいいか。どうせ接着剤を使うなら、ステンレスワッシャーに接着してしまえばいい。中央部にギアを設けたために、ブレーキ材のスペースが外周部に追いやられ、幅の狭い輪になってしまったので、接着しないと形状が保てないだろう。ならば金属用のエポキシ系接着剤で、紙のブレーキ材をステンレスワッシャーに接着すると同時に、その接着剤が紙に浸透することを期待しよう。
この部分のことは詳しく書かない。試行錯誤の長い道のりがあったが、結論だけを記録に残す。問題は紙の厚さだった。当初の目的は薄くすることだった。しかし薄すぎても問題が生じる。ピンを仕込むために3層構造化した一番上のステンレスワッシャーの下部のボビン部が、ギアを刻んだワッシャーのさらの下のワッシャーと接触するのだ。したがって程よい厚さを実現しなければならなかった。その厚さは約0.2mm。したがってもとの厚さと比べて、2枚で0.6mm程度の薄型化を達成しなければならない(=にとどめなければならない)。
最初に試したのは、クラフト封筒だった。漂白されていないクラフト紙は、強度に勝るから、摩擦に強いはずだった。しかしこれは薄すぎた。エポキシ系の接着剤で丹念にワッシャーに接着したはいいが、厚さが足りず、ワッシャー面と接触せずに隙間が開いてしまった。
次に試したのは、2つ折りの案内カードだった。厚さは十分だった。しかし紙質が上質過ぎて、接着剤の浸透が悪かった。より浸透性のよい瞬間接着剤をもってしても、ほとんど浸み込まなかった。接着剤が染み込まなければ、長年の仕様によりセルロース繊維が剥がれることが予想された。だからボツだった。
同程度の厚さで、浸透性のよいもの。何かないか? そこで思いついたのは画用紙だった。画用紙を輪に切り抜いて、ワッシャーに対してエポキシ系接着剤で張り付け、エポキシ系接着剤の粘度が高すぎて紙繊維全体に浸透しないのは、上から瞬間接着剤を染み込ませて補った。その記録が下の動画だ。
上の動画の最後で試しているとおり、クリックはきっちりと鳴った。成功だ。動画の途中で、ギアを刻んだワッシャーの裏表を間違えて音がうまくならなかったが、そう、この改造によってワッシャーには歯の向きによる表と裏の区別が生じたのだ。